Post by account_disabled on Mar 7, 2024 0:19:56 GMT -3
Ford Motor Company says it is expanding its 3-Wet paint capacity by 50 percent this year, adding the environmentally friendly process to four more plants on three continents. It expects the process to reduce CO2 emissions between 15 and 25 percent at those facilities.
Ford says it was the first automaker to implement the 3-Wet high-solids solvent-borne technology in 2007. It now has eight plants in North America, Asia Pacific and Europe equipped to use the process to paint vehicles. High-solids solvent-borne technology refers to a paint formulated to minimize solvents, resulting in a concentrated pigment and resin mixture with fewer volatile organic compounds released.
By the end of 2013, Ford will have implemented the technology in 12 plants. The automaker says it will expand to additional facilities worldwide over the next four years.
The 3-Wet process derives its name from three layers of paint applied one after the other prior to earlier coats having cured. The process eliminates stand-alone primer application and B2B Email List a dedicated oven required in the conventional process that was used before. Advanced chemical composition of 3-Wet paint materials allows for the three layers of paint — primer, base coat and clear coat — to be applied while each layer is still wet.
The process saves electricity from the blowers that circulate massive volumes of air through paint booths, and reduces Ford’s use of natural gas needed to heat the air and ovens. This results in reduced CO2 emissions, as well as reductions in VOC compared to current medium-solids and solvent-borne paints.
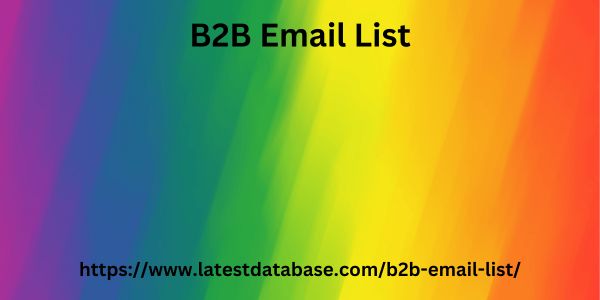
Since the pilot launch at its Ohio assembly plant five years ago, Ford’s global 3-Wet paint process has reduced CO2 emissions by 15 to 25 percent and VOC emissions by 10 percent compared to either conventional high-solids solvent-borne or waterborne systems, the company says.
In 2013, Ford will install the 3-Wet process at the following facilities: Flat Rock assembly plant, Flat Rock, Mich.; Kansas City assembly plant, Claycomo, Mo.; Jiangling Motors Co., Jiangxi Nanchang, China; and Valencia assembly plant, Valencia, Spain.
Last month, Ford announced it had reduced the average amount of water used to make each vehicle by 8.5 percent between 2011 and 2012, putting the company more than halfway toward its goal of using an average of 4 cubic meters per vehicle globally by 2015.
Ford says it was the first automaker to implement the 3-Wet high-solids solvent-borne technology in 2007. It now has eight plants in North America, Asia Pacific and Europe equipped to use the process to paint vehicles. High-solids solvent-borne technology refers to a paint formulated to minimize solvents, resulting in a concentrated pigment and resin mixture with fewer volatile organic compounds released.
By the end of 2013, Ford will have implemented the technology in 12 plants. The automaker says it will expand to additional facilities worldwide over the next four years.
The 3-Wet process derives its name from three layers of paint applied one after the other prior to earlier coats having cured. The process eliminates stand-alone primer application and B2B Email List a dedicated oven required in the conventional process that was used before. Advanced chemical composition of 3-Wet paint materials allows for the three layers of paint — primer, base coat and clear coat — to be applied while each layer is still wet.
The process saves electricity from the blowers that circulate massive volumes of air through paint booths, and reduces Ford’s use of natural gas needed to heat the air and ovens. This results in reduced CO2 emissions, as well as reductions in VOC compared to current medium-solids and solvent-borne paints.
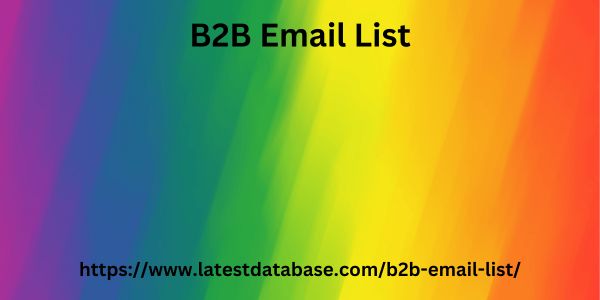
Since the pilot launch at its Ohio assembly plant five years ago, Ford’s global 3-Wet paint process has reduced CO2 emissions by 15 to 25 percent and VOC emissions by 10 percent compared to either conventional high-solids solvent-borne or waterborne systems, the company says.
In 2013, Ford will install the 3-Wet process at the following facilities: Flat Rock assembly plant, Flat Rock, Mich.; Kansas City assembly plant, Claycomo, Mo.; Jiangling Motors Co., Jiangxi Nanchang, China; and Valencia assembly plant, Valencia, Spain.
Last month, Ford announced it had reduced the average amount of water used to make each vehicle by 8.5 percent between 2011 and 2012, putting the company more than halfway toward its goal of using an average of 4 cubic meters per vehicle globally by 2015.